If you run a laboratory, you know that procedures written years ago to comply with older versions of the standards are the bane of your life. It’s challenging to work out if you can withdraw or rewrite them without somehow bringing down a load of non-conformances at the next assessment.
The latest versions of both lab accreditation standards (ISO 17025 & ISO 15189) require fewer procedures, but complying with a standard is only one reason to have written procedures or defined processes. So, it’s worth stopping to think about the purpose of your QMS.
6 Reasons for Having a QMS
#1 Define Repeatable Processes
The number one reason for a quality system is to standardise your critical processes so they are repeatable over time and by different staff members. These processes need to be repeatable not simply for the sake of it but because you have worked out the best way to do something.
Having a standardised way of doing a task gives you a stable base to work on improvements and a way to measure the effect of the changes you and your staff make to your processes.
Improvements are the whole point of quality management.
#2 Reduce Interruptions
There are specific tasks you do without thinking every day or every week. And there are also tasks you should do but don’t. You want to improve your processes, but you keep getting interrupted by staff who need answers so they can get on with their work.
We see this in some of the laboratory businesses we work with. The directors have grown the business based on their skills, but find it hard to get a day off because so much information is in their heads. To them, we say, you are not the sole fount of all knowledge. Write procedures, sure, but consider using signs and visual aids to bolster visibility of your processes.
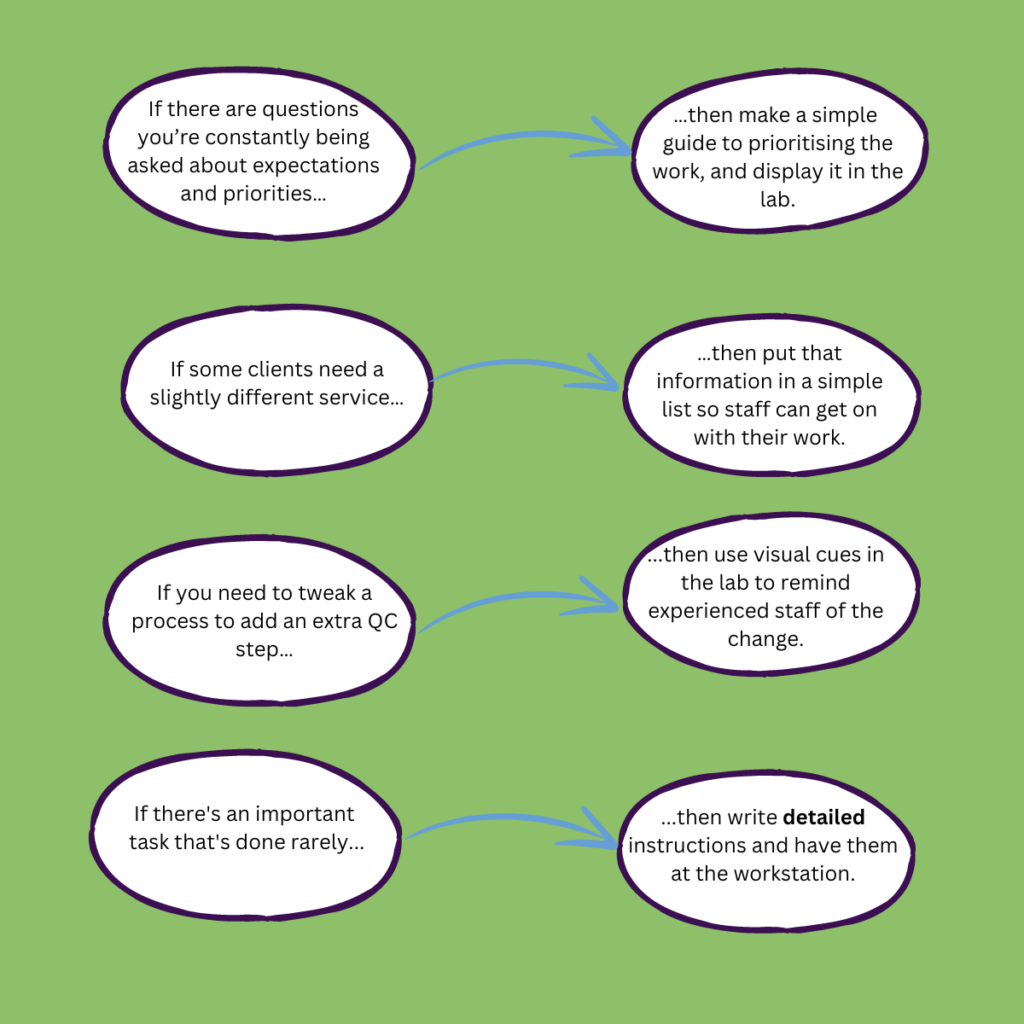
Don’t keep that knowledge to yourself! Display that table of reference information, label the shelves, mark out those workstations and keep records of tricky supplies and suppliers. Setting up a visual workspace and training your staff enables them to work independently. Here’s to fewer interruptions!
#3 Empower Staff
We tend to forget how much knowledge staff need to pick up in those first few days and weeks on the job and how intimidating it can be to ask questions constantly. Simple, straightforward “procedures” can underpin training programs. Give them to staff to read before they come to the bench, and training will be faster and smoother.
Don’t forget that procedures can be or include photos, videos, and diagrams. Think of them as setting the standard that you want your lab staff to meet.
They need to know what good looks like before they can try to get there themselves.
When you’re designing a QMS, a handy way to think about it is:
- Decide what processes you will train staff in – think about a complete process that you would want to be able to sign them off on
- Document these processes with enough detail so they can determine if they’ve done it correctly for themselves
- Set up your training records to align with these procedures/methods. There should be one procedure for each training module.
#4 Meet ISO Standards
Sometimes, this is what it comes down to. Your lab is accredited to an international standard; some clauses are mandatory. So instead of pushing back by saying, “This doesn’t apply to us,” ask, “How does this apply to us?” and “How do/can we manage this risk?”
The ISO laboratory accreditation standards were written with laboratories in mind, not accreditation bodies. Think of ISO 17025 and ISO 15189 as a list of all the risks to your laboratory business. While the standards focus a lot on risks to the quality of test results, they also cover general management and quality principles that can help move your laboratory from a reactive mode of operation to a proactive mode.
#5 Give Lawful Instructions
According to ISO 17025 and ISO 15189, you are responsible for providing the information people need to do their job.
So, if there are specific tasks that your staff MUST do, it’s best to document them. This can be in any format (procedures, signs, emails, meeting minutes, photos, videos) that conveys the information effectively.
#6 Sell Your Laboratory Business
If you own the laboratory business, you may want to sell it one day. To sell it as a going concern, you need to demonstrate that the laboratory not only meets accreditation requirements and safety obligations but it can also run without you and any other directors.
You may find this challenging as you need to define some management processes that may feel a little personal. Having an up-to-date QMS takes some of the stress out of that. You can hand over the procedures, and they can add extra details as they work them out.
Quality management systems are important.
Having a QMS can make your laboratory run better and help your staff feel more valued. And with fewer tasks falling to you, it may even mean you get that dreamed-of holiday… now wouldn’t that be something?
Need help bringing your quality system up to scratch?