Risks to impartiality are alluded to in both ISO 17025 and ISO 15189, but neither standard is really clear about what the sources of risk might be. These risks have always been around – they’re just more evident in some types of lab than others.
If you have identified possible risks to impartiality you will want some ideas on how to address them. Don’t forget to make the actions commensurate with the level of risk and likelihood.
What can be done to protect the reputation and integrity of your business? After all, reliability of test results is likely to be central to your business model.
Read on for a step-by-step approach to reducing or eliminating risks to impartiality.
8 ways to reduce risks to impartiality
1. Technology in testing processes
Removing the possibility for results to be changed or left out is a complex task that may require a number of measures to be put in place, such as the following:
- Processes to ensure that all samples are individually logged and sample numbers cannot be reused – e.g. bar-coded sample labels.
- Direct capture of test data in the lab – opt for testing and measuring equipment that can be hooked up to a computer to directly record readings without human involvement.
- Logging field data directly into the laboratory information system via phones or tablets.
- Remove manual steps from testing as far as possible – explore all options for automation.
- Ensure all results are transmitted directly “back to base”.
- Automated checks can include a comparison against expected results for that type of sample or previous results.
Don’t forget to make sure the data storage is secure and that there is an audit trail for any changes made.
2. Employment practices
Consider possible sources of motivation to alter test results. These can include bribery, not wanting to lose contracts, being nice to a favourite client or even just wanting to get lots of work done.
Many laboratories carefully screen job applicants to make sure they are not only a good fit for the type of work, but also that
- They have no connection to the industry they will be testing for (such as in drug testing).
- Employees aren’t holding jobs with competitors.
- They don’t have shares or other relationships that could present a conflict of interest.
You can simply get staff to sign a declaration when they start with you, or you may need to actively research if the risk is high.
3. Quality culture
Creating an ethical work culture must come from top management. Instilling a culture of openness, honesty and integrity goes a long way towards protecting your company’s reputation. These values need to be lived and breathed through the organisation at all levels.
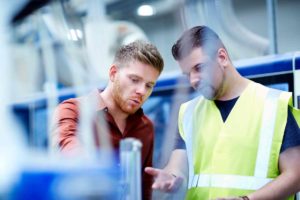
Start with your induction process and continue to emphasise your values throughout a staff member’s time with your company. Make sure they know that they can speak up if they don’t feel something is right. Talk about recent incidents or problems at regular meetings and encourage staff to hold each other to account.
Your quality system, which should be seamlessly integrated with the day-to-day work, is crucial to developing a culture of commitment to quality best-practice. Staff should know to look up your organisation’s methods or procedures when they’re not sure what to do.
This helps develop a “this is the way we do it here” culture. It also empowers staff as there is a clear process in place if they feel pressured to change results or test only at a specific location. Who should they report this to? When should they stop testing and leave the site?
Make sure your staff learn about these policies when they join your company and design opportunities to revisit the policies on a regular basis.
4. Checking data & reports
An independent review of results introduces a level of impartiality as well as the benefits of a fresh set of eyes for errors. An experienced eye can often pick up unusual results or trends.
5. The laboratory environment
The lab environment can influence the reliability of results. There are a number of ways you can reduce this risk:
- Provide a secure lab environment where the lab staff can work undisturbed by interested parties.
- Keep addictive or valuable materials in secure storage, requiring two staff members to access them.
- Try not to leave staff working alone for extended periods without interaction with seniors to support and mentor them.
- Install security cameras in specimen reception areas to reduce the risk of samples being interfered with (and prove chain of custody).
- Install security cameras in laboratories, particularly if there may be accusations of testing not done.
6. Managing Conflicts of Interest
Review the structure and reporting lines: look for potential conflicts of interest (such as results being used within your company). This can be an issue for production-related organisations and those involved in design engineering. Where possible, remove problematic reporting lines. For instance,the laboratory technician or manager should not report directly to the Production Manager or Design Engineer.
Potential conflicts of interest related to external relationships should be declared upon employment and confirmed again on a regular basis. (This particularly applies for company directors). Show that you are aware of these potential conflicts by excusing staff or management from certain projects or decisions as necessary.
7. Contract review
Technical review of contracts is critical in industries where pressure may be applied to get favourable results. Clients may want to minimise testing costs as they are seen as an overhead.
Checking the technical, as well as financial details of the contract will help make sure you are not left out of pocket or pressured to complete inadequate testing due to time or financial constraints. Similarly, over-testing can lead to a devaluation of the test results – “it doesn’t matter so much if one (or a few?) are not quite right”.
If a client insists on an inadequate testing regime, it might be time to reconsider whether you really need to work with that client. Some of our clients have taken this option and have a much happier life because of it.
8. Training and education
Make sure you and your staff are well-versed in the importance of the test results. If you have technicians who don’t understand why they’re doing the tests, they won’t place much value on them being correct. What happens if a structure fails and it is found that testing was not accurate? What if your product gets released and is found to be non-compliant?
Staff need to understand that the implications of failure at this late stage can be huge, sometimes leading to court action. To avoid this potentially disastrous scenario, your team needs to be prepared to identify and deal with a compromised result immediately. Any short-term pain from dealing with someone who doesn’t want the true result is no matter compared to the long-term consequences for your business.
Get extra help
We have been helping our clients assess the risks to impartiality since the changes came in with the new ISO 17025. We can give you peace of mind that you are doing what you need to without reinventing the wheel or making unnecessary wholesale changes. If you need this kind of help, get more details here or contact us via our contact page.