Internal auditors can be better at identifying process improvements than most managers – let me tell you why.
What a manager may never see
There are things that internal auditors see that a manager would never have known about if not for the audit program. These can include: tests failing and needing to be repeated; risky workarounds to compensate for poorly designed processes; retesting QCs until a result falls within spec; using calibration factors incorrectly; biased sampling; poor labelling practices; unsafe work methods; some staff having their own special way of doing a task; continuing to perform tasks made redundant by process changes.
Most of these you will never know about unless you directly observe them. So why does an internal auditor see them when the manager walks through the laboratory every day and does not see it? I can think of a couple of reasons.
When a manager strolls through the lab their mind is filling in the picture with all sorts of details that they believe happen in that lab. This is not the fault of the manager, this is being human. Unless they go into the lab with the intention of studying a particular process, they will likely see very little of interest.
When a manager arrives in the lab, they think, “I am the expert on this process,” whereas the auditor thinks, “I don’t know much about this process.” Neither of these is wrong, but they have a big effect on what types of questions are asked and how the answers are listened to. A good internal auditor approaches the audit with a child’s mind—curiosity and wonder.
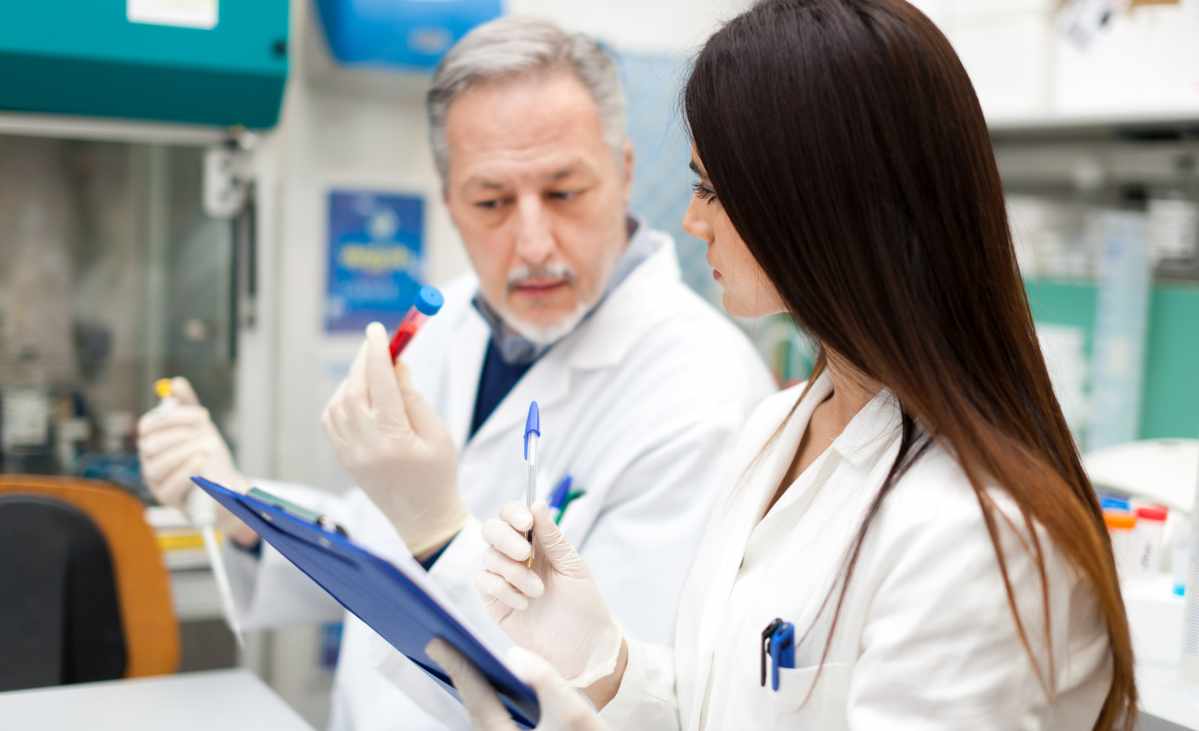
When an internal audit has been arranged, everyone is primed and ready to demonstrate and discuss the process. Time has been put aside and outputs are expected. There is a structure for collecting information and defining issues that need attention. And there is a rigorous system for following up on these issues.
Unless the manager has a very good rapport with their staff, staff members will not necessarily open up to them and may even modify their answers to what they think is the expected answer. Even worse, if they’ve opened up about work problems in the past and nothing eventuated, the level of trust may not be sufficient. There is an interesting paper on this from Harvard Business School.
A well-trained internal auditor can get alongside a scientist and really understand what they are doing and what the problems are. This is a privilege afforded to few outside of that particular laboratory.
So what are managers good for?
A manager’s role is to keep an eye on the bigger picture and enable their staff to do their jobs well. Many improvements introduced by managers are larger scale and therefore disruptive changes. This is not a bad thing, but the continuous small improvements that are generated through internal audits or handled in the non-conformance system can also lead to sustained improvement. They are easier to implement and to check for unintended consequences without getting to a point of no return in the project. Whereas introducing a new LIMS entails a myriad of changes and limitations that can end up slowing down your workflow as you try to cope with them.
Benefits of a good internal audit program
There are real benefits that can come from a well-designed internal audit program whether non-conformities like the ones above are found or not: staff learn how their up- and down-stream customers work & what their difficulties are; they gain confidence to talk about their work and the purpose of it; auditors improve their knowledge of the quality system; improvement suggestions arise from an ‘outside pair of eyes’ reviewing processes; better standardisation of lab processes; risks identified and documented; effective identification of root causes; staff learning how accreditation/certification requirements apply in their area; and so on.
Not seeing the benefits? Help is at hand
You may be the lab manager and doing all of the internal audits, or you may simply have run out of ideas on how to get value from audits. If you would like to get more from your audit program, O’Dwyer Accreditation can help. We offer expert internal auditing services so you can get the best benefit from your resources. Or we can review your program and help you implement a different approach with training and mentoring services.
We run training on internal auditing and audit programs. Check it out here, or book a free mini-consult to discuss your situation with Cathy.