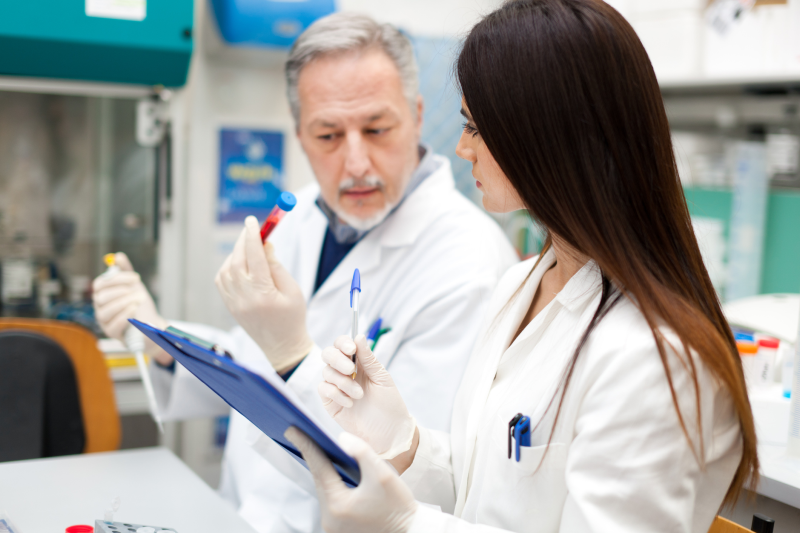
Banish compliance confusion
and make your quality system work for you with a …
Quality System Reset
Is this you?
You’re not alone. Many NATA-accredited labs look to professionals for help trying to understand NATA compliance. Professionals like O’Dwyer Accreditation.
At O’Dwyer Accreditation, we not only help you make your quality system NATA compliant, but we also help you turn it into a tool that creates genuine improvements in your laboratory business.

Quality System Reset
Introducing the Quality System Reset, a proven process that will enable you to develop your quality system to fit your business, so you can get back to what you do best – helping your clients with world-class testing.
With our Quality System Reset, you’ll learn how to:
- meet accreditation requirements without compromising efficiency
- get results from your quality system so you start to see real improvements
- understand how your systems meet requirements so you can welcome NATA with confidence
- work out which procedures you really need so you can spend less time administering a document control system.
We engaged O’Dwyer Accreditation because of their extensive experience in the area of NATA preparations. Working with them was so easy, despite the very difficult and intense nature of NATA accreditation. The whole process was great, and we now have an extensive list of tasks to complete and an action plan that makes it all manageable.
Sue Anderson | Technical Services & Compliance Manager | Farm Pride
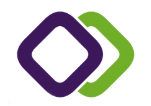
Bring your quality system into the present
It’s natural to follow processes the way you’ve always done, and not think about whether all those steps are even necessary.
But an outdated, complex or irrelevant system is a barrier to staff engagement, and can even cause problems for NATA-accredited laboratories.
It’s important that your system:
- informs management when significant issues or worrying trends arise
- drives real improvements to the way the lab works
- gives your staff the information they need to do their jobs effectively
- escalates risks to the right people.
If you’re working in a system that you know is not functioning well on a number of fronts, it can be hard to identify what needs to change first. With a full review of your quality system, including communication channels and outputs, we can help you prioritise your improvement efforts so the task becomes manageable.
We’ll partner with you and your management team to develop a plan to get your quality system humming.

How it works
Scope
First, we meet so you can tell us what’s on your mind, and we can be sure we have a good handle on your worries and priorities.
Site visit
We’ll visit your lab to see it in action and identify any areas for improvement…some of which you may not have thought of.
Report
We report not only on what you need to do to meet your accreditation requirements but also on processes to make your system run smoother. These are all the details and advice that NATA is unable to provide in their assessment reports.
Our report shows you where to focus your efforts (and those of your senior staff) to achieve real improvements and how to implement effective changes.
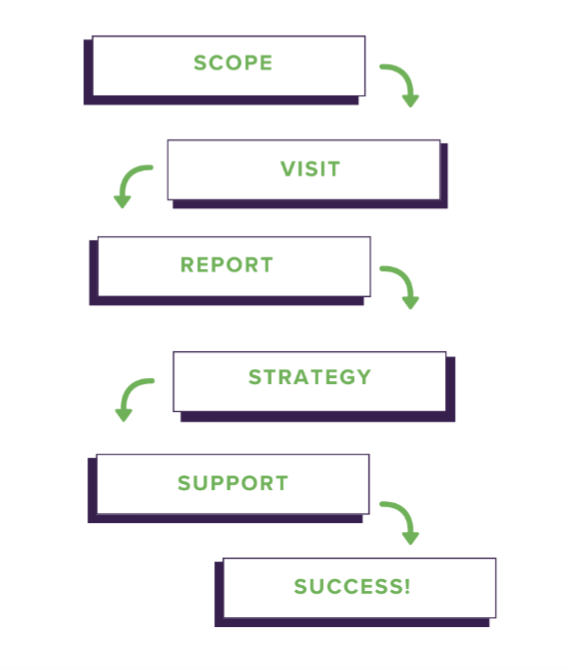
Strategy
Your report comes with a clear action plan aligned with your priorities and where you are in the accreditation journey. You’ll discover how to address key issues that will give you the results you want – whether that’s strengthening your systems to achieve real improvements, streamlining compliance activities, or modernising your processes.
This enables you to move ahead, confident that your efforts will meet accreditation requirements and improve your lab’s efficiency.
Support
We meet with you within a month of your Quality System Reset Report to discuss our findings, and help you plan the best way to implement our recommended changes. This means you have all the support you need to act on them, and not just file the report away in a drawer.
And we’re available for follow-up questions – once we know your system, we can quickly help with accreditation-related questions.
Success!
After completing your Quality System Reset you can be confident that your lab will not only be compliant, but your quality system will be easier to manage. That’s because we look at your quality system as a whole to ensure it remains relevant to how your business operates on the ground. As well as ensuring your lab is compliant, we make recommendations to streamline your processes, so that they include only the steps that your business needs. No more tasks to be completed ‘just because.’
And because your report can also form part of your audit records, that’s another audit ticked off for the year (or several, probably). Bonus!
We engaged O’Dwyer Accreditation as consultants on our application for NATA accreditation. They were very helpful, and their advice and coaching certainly contributed to us being granted accreditation.
Lou Harpur | Statewide Laboratories Pty Ltd
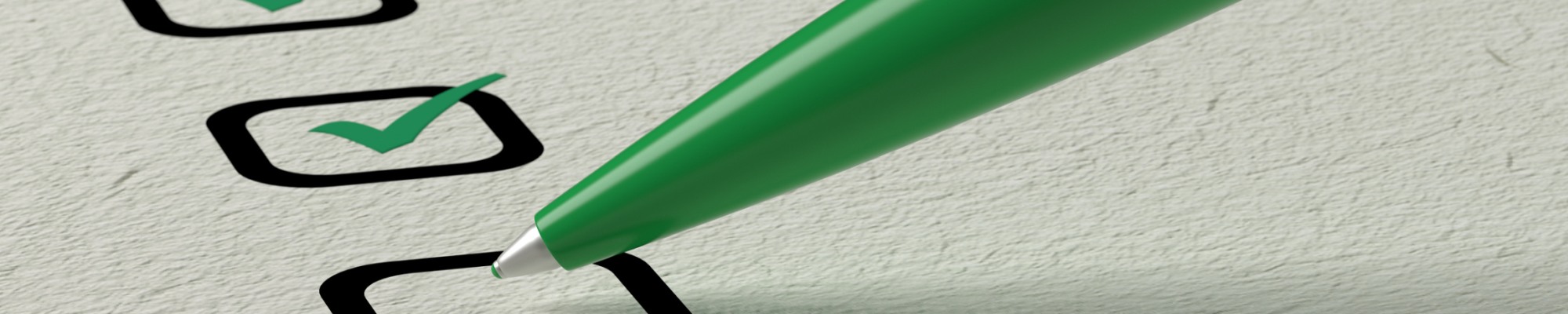
Stop wasting time on unnecessary documentation and tasks.
Of all the quality management systems we’ve helped clients with, we’ve found that most of them (around 70%) have one or more of the following issues. Their documents may:
- be completely over the top for the size of the business, with hundreds of documents to maintain
- say almost nothing about how they generate value and how they maintain quality in the process
- be off-the-shelf or copied ‘systems’ describing someone else’s business (or, worse, no one’s business)
- have been relevant and up-to-date years ago but now describe something that no one remembers
- not cover many of the laboratory functions or accreditation requirements.
After you’ve worked with us, you will walk away with lab quality systems that are relevant, concise and useful.
We have used O’Dwyer Accreditation to conduct our internal audits for nearly ten years, and working with them is always an excellent experience. They are friendly, practical and constructive, and help us work towards improving our quality systems while ironing out the occasional glitch in the system!
Tony Bergen | Managing Director | Australian Photometry and Radiometry Laboratory
Our Guarantee
O’Dwyer Accreditation has been helping Australian laboratories meet their NATA accreditation requirements for over 20 years. Whatever problem you have with accreditation, we’ve not only seen it before, but we’ve solved it for countless others in your situation. We’re so confident in our expertise that if any of our recommendations lead to a nonconformance from NATA, we’ll guide you through correcting it without any further charge.
Our team of professional accreditation consultants can help you confidently develop your business and maintain your NATA accreditation.
Take your lab from unsure to compliant & confident
We offer a limited number of Quality System Resets each year (yes, our dance card is often full). Book now so you can be sure to lock in our Quality System Reset to meet your quality schedule. You’ll approach your next assessment with confidence.
And don’t forget the sooner you have your report, the more money you will save by streamlining your systems.
What does it cost?
We’ve done Quality System Resets for scores of labs, so we’ve developed the most effective way to bring your lab up to standard.
Our legendary service includes:
- key recommendations to safeguard your NATA accreditation
- recommendations to improve your systems
- an overall assessment of the effectiveness of your communication and reporting systems
- a detailed report with actionable items that you can work through independently
- a follow-up meeting to help you keep moving.
Your investment in a Quality System Reset: $3,168 (ex GST).
Invest in your long-term compliance journey with an optional GAP analysis
Do you think or say these things during or after each NATA assessment?
- I’m sure we have that documented somewhere.
- We’ve had this discussion with assessors in the past – how did we answer it then?
- I don’t see the problem – why are they telling us to do x?
Then maybe what you need is a GAP analysis.
With our detailed GAP analysis, you will be able to use it to
- educate and inform your staff members about HOW your systems meet the accreditation requirements
- answer questions more effectively during the assessment, reducing the number of findings in your report
- respond to the assessment report with clear evidence of how you meet particular requirements
Add a GAP analysis: $990 (ex GST).
Still not sure?
Download our eBook on Nailing NATA Assessment Responses to guide you through your next “round” with NATA.
Browse through our most popular blogs.