Why all lab managers should fully embrace the process approach outlined in ISO17025, ISO9001 and ISO15189
No email-free holiday in years? Scared to take a day off?
Alarm bells should be ringing.
It may be the last thing you want to hear, but if you are overworked, always too busy or want bigger things for your laboratory business, there is one thing you really need to start doing. Now.
To reduce the risk and burden of one person holding too much responsibility in your organisation, you need to fully embrace the process approach.
You know the term well. It pops up all through ISO 17025 and 9001 but perhaps you’re not too sure what it means? It’s more than just quality-compliance jargon. It’s a piece of quality wisdom that will help you spread the load of leadership in your organisation.
It’s your ticket to greater freedom in your management role.
Freedom to think big, but also freedom to take a break or step aside.
Pay-off for pro-active managers
In many years helping labs design, tweak and implement optimal quality systems that meet (and exceed) NATA’s expectations, I have seen first-hand that a bit of lifting early on has a surprisingly big-pay off later.
The trouble is, managers often don’t believe what is possible or don’t know where to start with what may seem like big or difficult changes. As a result, they unconsciously hold on to knowledge that should be shared.
Starting with a proven strategy for improvement – the process approach – will help you get the ball rolling. You’ll begin to move towards new possibilities you previously couldn’t see on the horizon. Not least – freedom to take a solid break!
The process approach in a nutshell
The process approach is a management strategy in which managers decide on, “manage and control the processes that make up their organisations, the interactions between these processes, and the inputs and outputs that tie these processes together.” (The Process Approach, Praxiom Research Group)
This means every process has a reason behind it and no process occurs in isolation to the whole, or without being reviewed. Learning how to see your laboratory business as a series of processes instead of a series of departments, people or isolated tasks is liberating. It becomes easy to see what is happening and how to measure the success of it.
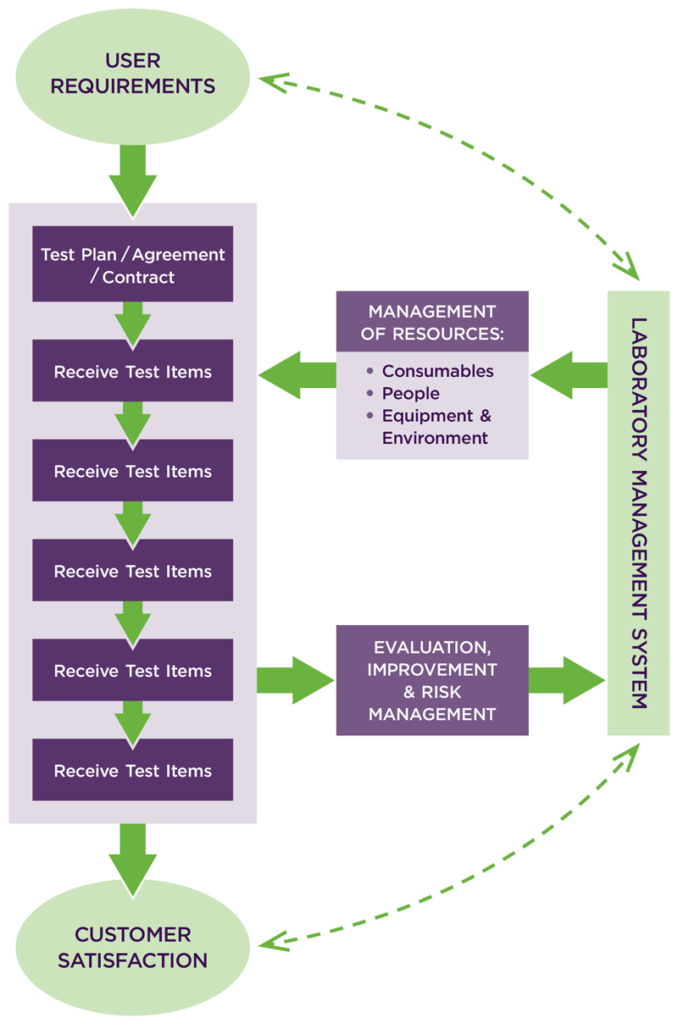
A process diagram for a laboratory looks something like this:
The inputs to the whole process are user requirements, and the outputs are customer satisfaction. Each step in this process can also be treated as a separate process, and measures put in place to make sure they are working effectively. When aligned with the organisation’s vision and communicated effectively to staff, the process approach boosts staff engagement and performance by giving your staff more responsibility and more opportunity for recognition.
This enhances intrinsic motivation and initiative among staff, making you a happy and proud manager who is free to walk away and take a break.
Tip: Many managers get into a habit of holding important information in their heads or just not adequately training up other senior staff to take over the reins. This is both a business risk and an unnecessary burden on you.
Stay tuned for our follow-up post on this topic : 4 Steps to Reducing Reliance on Constant Management Oversight
Check out our courses and consulting services below if you or your staff require extra facilitation to implement the process-approach and improve your quality system.
The Best-Practice Internal Audit Program Your Lab Needs
Or sign up to our email list for regular tips and insights about how to get the most out of your accreditation.